Introduction
Japanning within the context of a furniture finish, refers to finishes that are usually in the form of a dark, complex lacquer. It emerged as a finish in the 17th century after Oriental lacquered objects were imported into Europe in the late 16th Century.
A great number of materials were employed for the manufacture of japanned objects. This was an evolving technique based on new development in furniture finishes in the 17th and 18th centuries. A typical structure for a japanned surface is a combination of base, ground, varnish and decoration layers. These layers can be made of various materials, such as wood, leather, natural resins, alcohol, oils, pigments, metal leaves and powders. In the beginning the most common base material for japanned furniture was wood. Almost all japanned surfaces produced in the late sixteenth century were made from spirit varnishes, that is, natural resins in alcohol.
Decoration layers were often made of metal leaves and powders, or gold paint, depicting chinoiserie scenes. Later, in the eighteenth century, tinplate and papier mâché were primarily used as substrates, and were covered with the more durable and resistant oil varnishes (natural resins in oil). Polychrome floral designs became the common form of decoration. Japanned furniture pieces have a reputation for being fragile, brittle and often subject to damage from environmental factors like humidity and expansion and contraction of the base timbers.
What is Japanning?
Although often referred to as lacquer, it is distinct from true East Asian lacquer, which is made by coating objects with a preparation based on a dried native Asian tree sap which was not available in Europe. Japanning is most often a heavy black "lacquer", almost like enamel paint. Black is common and japanning is often assumed to be synonymous with black japanning.
The European technique uses varnishes that have a resin base, similar to shellac, applied in heat-dried layers which are then polished, to give a smooth glossy finish. It can also come in cream, reds, greens and blues.
The japanned technique employed the use of varnishes, which created a similar appearance to lacquer when applied in a certain way. One such option was shellac, which was made of spirits of wine used as a thinner and combined with a catalyst.
The technique to create japanned furniture took many steps and a great deal of patience for the craftsman. Japanned furniture often started as a wooden carcass that would then be laid with muslin and a gesso ground. If the craftsman wanted to added three dimensional relief for certain decoration, such as a pattern or artistic effect, the gesso could be applied for this purpose. At this point, the surface could be painted in the desired tempera colour, usually black, red, or blue, followed by a layer of clear or pigmented lacquer.
The surface would then be dried and polished. Further layers of lacquer could be applied in between polishing the surface, often requiring up to twenty additional layers. Just before the application of a final layer of a clear coat of lacquer, the craftsman could apply gold and silver decoration as highlights.
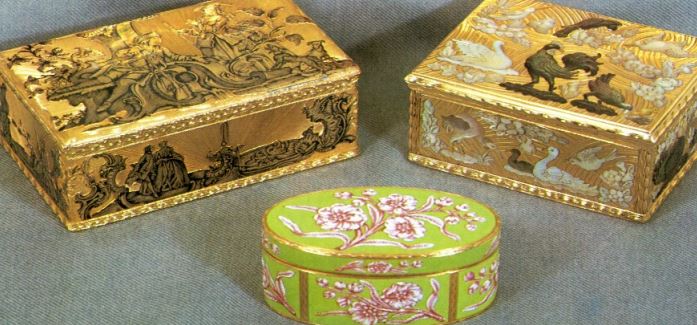
Decoration
As far as the decoration itself was concerned, there was a concerted effort by early craftsmen to directly copy designs from China and the East. China was highly regarded for its association as a site of eternal wisdom (and the home country of Confucius). Porcelain, textiles, wall hangings, as well as lacquer pieces, were used as sources of inspiration for the decorative schemes. Other sources included illustrations of trips and missions in Asia by travelers.
Although Asian lacquer was highly prized in the 17th and 18th centuries, there were instances when the European Japanned furniture was deemed better than the original. In fact, Voltaire once famously remarked about French Japanning, known as vernis martin, ‘Ces cabinets ou Martin, A surpassé l’art de la Chine.’ (These cabinets or Martin, A surpassed the art of China).
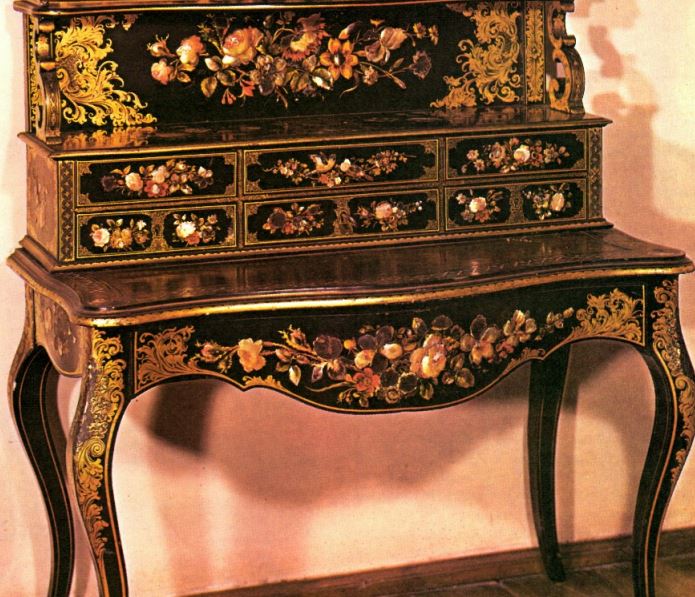
Japanning Tools
A further development in the workshop was the use of the Japanning technique to protect and preserve metal objects including metal tools. Ironware was japanned black to render it rustproof and even suitable for carrying water in some applications.
Stanley tools and others used it on the finished surfaces of the main casting of their metal planes and frog, that is, a Japan varnish. Whilst most of the applications were artistic in nature, many craftsmen valued the preservative nature of the finish on their metal tools to protect the surface from the deleterious affects of moisture and chemicals. In fact Ford Motor Company used it as a finish on their automobiles in the early 20th Century.
At the basic level, the application to metal objects is a mixture of linseed oil, turpentine, and a powdered or crystalline form of a specific type of asphalt product called gilsonite. There are as many recipes for Japanning that have been documented over the years, but these too have evolved as new forms of finishes were discovered.
The best results come from a baking process after each coat to about 200 degrees for an hour or two. This process does require a well ventilated area due to the toxic fumes that are generated through this process.
Article submitted by Don Jones, Carbatec Customer Care Team.
As a restorer and preserver of beautiful furniture, Don often sees the results of years of neglect or misplaced good intentions on caring for wooden furniture of all ages. Whether you are caring for a 100 year old antique, a new purchase or something you have created yourself, Don shares some insight into caring for your furniture.
Click here to download a copy of Don's Japanning - Traditional Finishes Series