You have just unpacked your latest purchase... a beautiful Carbatec 15" thicknesser. You've cast aside the unread manual and have dived head first into assembly. All bolts tightened, blades aligned, and we head straight for the pile of waiting timber. What a magnificent collection of exotic hardwood, just pleading to be converted into a three meter long dining room table. You plug in your new weapon and you throw your first victim to the spinning blades.
It's hard to recall what hits you first, the ear piercing scream of the blade hitting solid timber, then the mulching (and re-mulching) of the waste material, or the fact that the workshop (and half the neighbor's workshop) starts to rapidly fill with re-mulched hardwood shavings. As you cough up some dust, you think to yourself, "Pity the quality of the milled finish isn't exactly what I expected."
Importance of Dust Extraction
Professional workshops have known for decades that one of the most important pieces of machinery in the workshop is an adequate extractor. It's only us serious DIYers that seem to question their wisdom. A clean, dust-free workplace is not only safer, but far less work in the long run. There is less cleanup and less airborne dust, which is very important when it comes to the finishing stage. Another important fact is that it is far better for your machinery to have this dust and shavings removed. Other then being forced back around the cutting area and affecting the quality of the work, fine dust particles can be sucked into electrical components, build up on moving parts or pile up in areas underneath your machinery (becoming a fire hazard in the process). Worst of all, these particles can find their way into your lungs. Dust extraction is NOT a replacement for PPE (Personal Protective Equipment,) but if it reduces the dust in your immediate work area, it means your PPE is going to work much more efficiently too. The sad fact is that running machinery without dust extraction may affect your warranty if something does go wrong. Why didn't I read the manual?
Extractor vs. Vacuum Cleaner
Most workshops have access to a vacuum cleaner, either a dedicated unit or the better half's household unit (only if you don't get caught)! They're great for cleaning the car and even getting the dust off the floor of the workshop. Isn't it annoying when a little offcut or long splinter gets stuck in the hose? You hear the motor start to struggle and whine and you proceed to wave the end of the hose around in some strange ritual that will hopefully dislodge the offending piece. So what makes us think that by hooking this same vacuum to a heavy-waste producing machine that the results are going to be any different? It really comes down to a simple rule - vacuums are made to vacuum and extractors are made to extract. Vacuum cleaners work on the principal of a low volume of air traveling at high velocity, while extractors work on high volume air, traveling at low velocity. Vacuums are great for lifting small quantities of fine dust from the bottom of your carpet through a small diameter hose. Dust extractors, on the other hand, are designed to cope with the quantity of waste constantly being produced, and the large diameter hose means no blockages (provided you have ENOUGH air volume). Air volume is measured in cubic feet per minute (CFM), and even a small, basic 1HP extractor is going to give you 600+ CFM of air flow. Most cutting/drilling machinery will require at least 600CFM of extraction. Edge planers or jointers need slightly more (depending on size), but large milling machines such as thicknessers will require at least 800-900CFM at the extraction point on the machine. This is an important consideration before taking the plunge.
Flexible Hose
Most woodworking machinery will be provided with a large diameter extraction connection. This will usually be a 4" or 5" (100mm or 125mm) connection. This should marry nicely to your dust extractor, either directly or with some form of adaptor. An important factor in the operational efficiency of your dust collection system is the positioning of the dust collector, in relation to the machine. Many people have designed elaborate systems, utilising Y-pieces to increase the quantity of machines connected, blast gates (switches to close off the air flow to one of more points), and running many meters of flexible hose up the wall, and across the ceiling, back to the extractor.
When they switch the system on, they wonder why the suction at the far end is barely enough to be audible, never mind suck several kilos of timber waste. For every meter of flexible hose you run, you are going to lose approximately 10-20% of your volume (CFM), and for every bend and fitting, you are going to lose a even more CFM. Do the math - just three meters of flexible hose, and a third of your suction is gone... but where? Have a look at the diagram below.
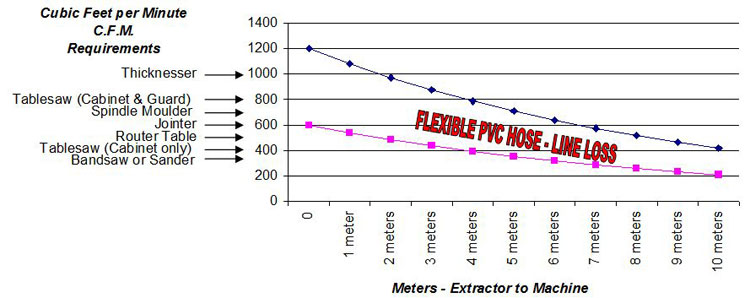
Have a close look at the flexible hose - every single ridge of the hose that the air has to run across is disrupting the efficient flow of the air, and in turn, the waste. If you want to run a larger system, make sure you have enough suction volume at the start, to ensure you don't run out at the business end. Professionally designed and installed workshop systems use rigid metal pipes, with a smooth finish and engineered bends to increase efficiency, and they run very high capacity dust extractors which will allow all machines to be run at the same time. Suction loss on these systems is usually only about 1-2% per meter, but the purchase and setup cost is very high. The straighter and simpler (and shorter) you can keep your home extraction system, the better. Remember that bigger CFM is always better.
Dust Extractor Safety
One hazard that is often overlooked in dust extraction equipment is the danger of the buildup of static electricity. The dry timber particles rubbing the inside of the flexible hose are constantly building a static charge, in the same way rubbing a plastic comb through your hair (if you have any) will build up a static charge. Static, when it discharges as a spark, is just one of three parts required to create an explosion. The other two parts are a fuel (in the form of fine dust particles), and air (which is being forced through the system). Explosions in dust extraction systems are rare, but they do happen. More often it's the large painful 'Crack' of the static finding its way to our finger tips that reminds us of this potential danger. A simple solution to avoid this situation is to ground your system. Fitting a grounding kit to the inside of the flexible hose and connecting the wire to both the machine and the dust extractor will minimise or eliminate static from the system.
Selecting Your Dust Extractor
Determining which extractor is right for you will depend heavily on what you want to do with it. If you only want to hook it up to your table saw, a very basic unit will do the job. However, if you want to connect it to your thicknesser or jointer, you need to start at a 2hp unit with a higher CFM rating and a larger waste holding capacity. It's important to think ahead about what your future requirements will be. If you're planning to add more machinery later and you don't want to move your extractor between machinery, invest in a larger unit that will allow you to add extra points without sacrificing too much performance. Be honest with yourself and it won't end up costing you more in the long run.
In the next blog we'll discuss extraction options, standard extractors vs. cyclone systems, easy improvements, performance upgrades and basic design.
Click on the links below for information and pricing on: - Dust Extractors - Dust Collection Accessories
|