Written by Tony Forbes, Maxis Distribution Brand Manger.
In the last edition of this article, I discussed the advantages of dust extraction, over the ever popular airborne / gravity operated option. I also compared dedicated dust extractors to shop-vac style vacuums, and showed how borrowing the Dyson and trying to cover up the fact that you did is not always the best option. Happy spouse = happy house.
In this edition I would like to expand on the subject and offer some direction for designing small workshop extraction systems.
First, we need to look at requirements, specifically considering which machines you have and which machines you plan to add (the latter being the thing most people forget to take into account). Each type of machine has a certain airflow requirement for effective dust extraction. We touched on this last time with our graph that illustrated the loss in suction through flexible hose (click here to refer back to this article).
A very basic list of machines and their minimum requirements would be as follows:
- Bandsaw: 300cfm
- Tablesaw: 400cfm (cabinet connection only)
- Router Table: 500cfm
- Jointer or Small Thicknesser: 600cfm
- Spindle Moulder: 700cfm
- Tablesaw 800cfm (cabinet and overhead guard)
- Lathes 800cfm
- Large Thicknesser: 1000cfm
These requirements are approximate and are of course heavily dependent on your usage and the type of material being used.
But what about an existing system you want to refine? Go back to basics, strip out some of the fittings, straighten the lines and simplify the whole design. A couple of percent here and there will help.
Note also that these specs refer to the extraction requirements at the machine (where the hose meets the machine's dust port), not the listed capacity of the dust extractor. To work this out you need to take into account the distance between the extractor and the machine, the machine type and the type of ducting used (flexible or rigid), as well as fittings, bends, etc. This way we can calculate an approximate line loss value across the entire system. Now is a good time for you to get out your crayons and paper. I will wait...
Planning
You need to do a good scale drawing of you workshop layout, position your machines in their ‘in-use’ location, figure out how you want to connect them, and decide where your dust extractor will reside. Try to keep the heavy producers of waste (like thicknesser, lathes etc) closer to the extractor. Draw out your desired plan, keeping the main line as straight as possible. List your ‘Y’ Junctions, ‘T’ pieces, connections, bends and blast gates, and total your hose requirements. To calculate you approximate line loss across your system, use the following rules of thumb:
- Every meter of 4” (100mm) flexible hose will reduce your CFM by around 7 - 10% per meter. Keep it short.
- 90deg bends will restrict airflow by 3-4% each.
- ‘Y’ Junctions will divide the airflow in half if both sides are left open (use blast gates to switch off the unused side). A gated “Y” Junction will reduce airflow by around 1-2% each.
- “T” pieces are fairly inefficient compared to “Y” junctions. They will reduce the airflow by 3-4% each.
- Stepping down to a smaller diameter, will increase the velocity but will lower the CFM airflow considerably. A good example would be trying to suck a lung full of air through a straw (one that’s not currently dipped into your favourite drink). It works, but it's hard work and you wouldn’t want to do it all day. Your future or current dust extractor agrees. Use minimal reducers, and try to keep them near the end of the line, near the machines that product smaller amounts of dust (scroll saws, mitre saws etc).
- KEEP IT SIMPLE
Armed with these guidelines, crayon in hand… develop a plan to reduce your dust.
Other Options for Ducting
We have been focusing our attention on flexible PVC ducting, but in the last issue I briefly mentioned metal ducted networks. Largely because flexible PVC is such a cheap and simple option, metal ducting has been out of the reach of most small workshops or backyard sawdust manufacturers. Carba-Tec have been busy developing a great value offering designed for just this market. We have been working closely with Eximo-Speedlock to put together a versatile DIY metal ducting network that will marry easily to exiting flexible networks, or make a great starting point for a new setup. We have chosen Speedlock for their respected reputation in the industrial market and their understanding of the special requirements that the DIY market has.
The efficiencies you gain with rigid ducting versus flexible PVC are dramatic. Using our rules of thumb listed above, with rigid ducting we'd now have:
- line loss will be only about 1% per metre
- 90deg bends will restrict airflow by only about 1% each due to their larger radius and constant diameter
- ‘Y’ Junctions will still divide the airflow in half if both sides are left open (use blast gates to switch off the unused side). A gated “Y” Junction will reduce airflow by around 1%
- “T” pieces are not used with rigid ducting due to their inefficient properties
- Stepping down is usually done through a long conical reducer which is far more efficient. We still recommend placing these near the end of the system.
The sort of rigid ducting network we're talking about here would have enough straights, bends, corners, junctions and fittings to put together a pretty substantial and professional dust system in a workshop up to about 6 meters long, with 3 outlets. Overall, you'd be looking at losing only about 15-17% total CFM. The equivalent system in flexible PVC would reduce your CFM by about 70%.
Eximo-Speedlock systems are very DIY friendly, are adaptable (extra components can be added or removed at any time) and are more affordable then you may think.
Types of Dust Extractors
Technically speaking, the commonly used dust extractors in our market are broken down into two main categories: baffle chamber and cyclonic separation. There are many variations on a theme, but usually these two are what you will find.
The more common and less expensive Baffle Chamber (or standard bag type) dust extractor uses a motor to spin a centrifugal impeller that - through its clever blade design - sucks air in through the centre of the fan and pushes it out toward the sides of the fan. Manufacturers design extractors so that the inbound waste follows this air path, through the impeller and into a collection chamber. The change in air direction once we get to this chamber (and gravity helps here), causes the heavier waste to fall down, and the lighter dust particles to rise up. These are caught in a filter on the top. This filter can be either a cloth or felt bag or a more elaborate pleated filter cartridge.
Cyclonic Separation is not a new concept. It has been available for industrial use for many years but has only become accessible and affordable to the general public within the past decade. Cyclones differ from standard bag extractors in many ways. Their design and build is far superior and the technology involved is far more efficient. Again, a motor is used to spin a centrifugal impeller, but whereas the impeller on the standard bag extractor was in line with the waste flow, the cyclone has two different paths. The airflow path pulls the waste into the collection chamber, but from there it uses directional baffles to divert waste material. Basic theories of thermodynamics and some high end aspects of quantum physics come into play, and effectively the waste flow path sees the material spun rapidly around the outside cone and it's then forced down to the bottom of the collection chamber, leaving the airflow path free of heavy waste. The remaining fine dust particles are then sucked through the impeller, and pushed out into a small collection bag. To explain this little better I have provided both this simple cyclonic separation formula, and a diagram.
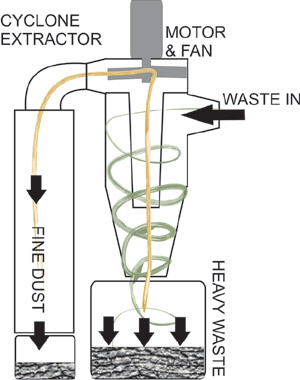 |
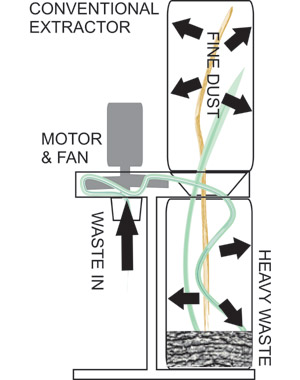 |
Cyclonic machines run consistently with maximum efficiency and constant air flow... |
...while traditional baffle chamber type extractors run less efficiently, with airflow being affected by the various factors we've already looked at. |
Quite simply, the main difference between standard bag and a cyclone is performance. Cyclones run at lower CFM rating than equivalent bag type extractors. This is due to the extreme efficiencies gained in the design. No longer is the actual CFM reading jumping up and down, due to the heavy waste material bouncing off and running through the impeller. The suction pressure being applied to the system is constant and uninterrupted. Cyclones efficiently deal with the heavy waste material and separate this from the fine dust.
Performance Enhancements For Existing Systems
On a standard bag system the fine dust is pushed up and is forced into the fabric filter bag. This fine dust needs to be cleaned occasionally by hitting the outside of the bag or by blasting it with compressed air. Maybe replacing the tired old filter bag would breathe some life back into your extractor? After-market cartridge filters can be added to most standard bag type extractors. These cartridge filters (which look like a very large car air filter) replace the standard fitted top filter bag and improve the outward airflow. Their greater surface gives the fine particles a larger area to settle into, and most cartridge filters will have internal cleaning brushes to aid with periodic maintenance.
In-line dust separators are available to reduce the volume of waste material before it gets to the impeller of your dust extractor. These usually sit on top of a large plastic rubbish bin, in line before your collector. These work quite well but will affect the CFM airflow as mentioned earlier.
Upgrading your existing flexible PVC network to a rigid system will be a huge enhancement. The cost of this upgrade may well be less then buying a larger extractor and plugging it onto your inefficient flexible PVC network (for little or no increase in performance).
So What is my Best Option?
There is no right answer, but there is always a wrong answer. The best option for both collection networks and dust collections is always going to be dependent on you own collection of machinery, how big your workshop is and where you see yourself in a years time. The wrong option is deliberately designing a system that’s ‘just enough’, or not quite enough to do the job. The money you save now will soon be forgotten when it comes time to fix the problems.
For all your extraction requirements, Carbatec stores stock a large range of dust extractors, cyclone extractors, flexible PVC, rigid ducting, PVC and metal fittings. Maybe the best option would be to talk to one of our professional staff and ask for some advice. If you have a large workshop or you’re a club with a complicated setup and you’re looking for a large ducted system, we can organise a professional designer to call and discuss options. They can calculate your requirements, design and install entire systems.
Click on the links below for information & pricing:
- Cyclone Dust Extractors
- Dust Extractors